Piping Design and PED compliance
in Chemicals, Discipline Engineering, EPCm
Share
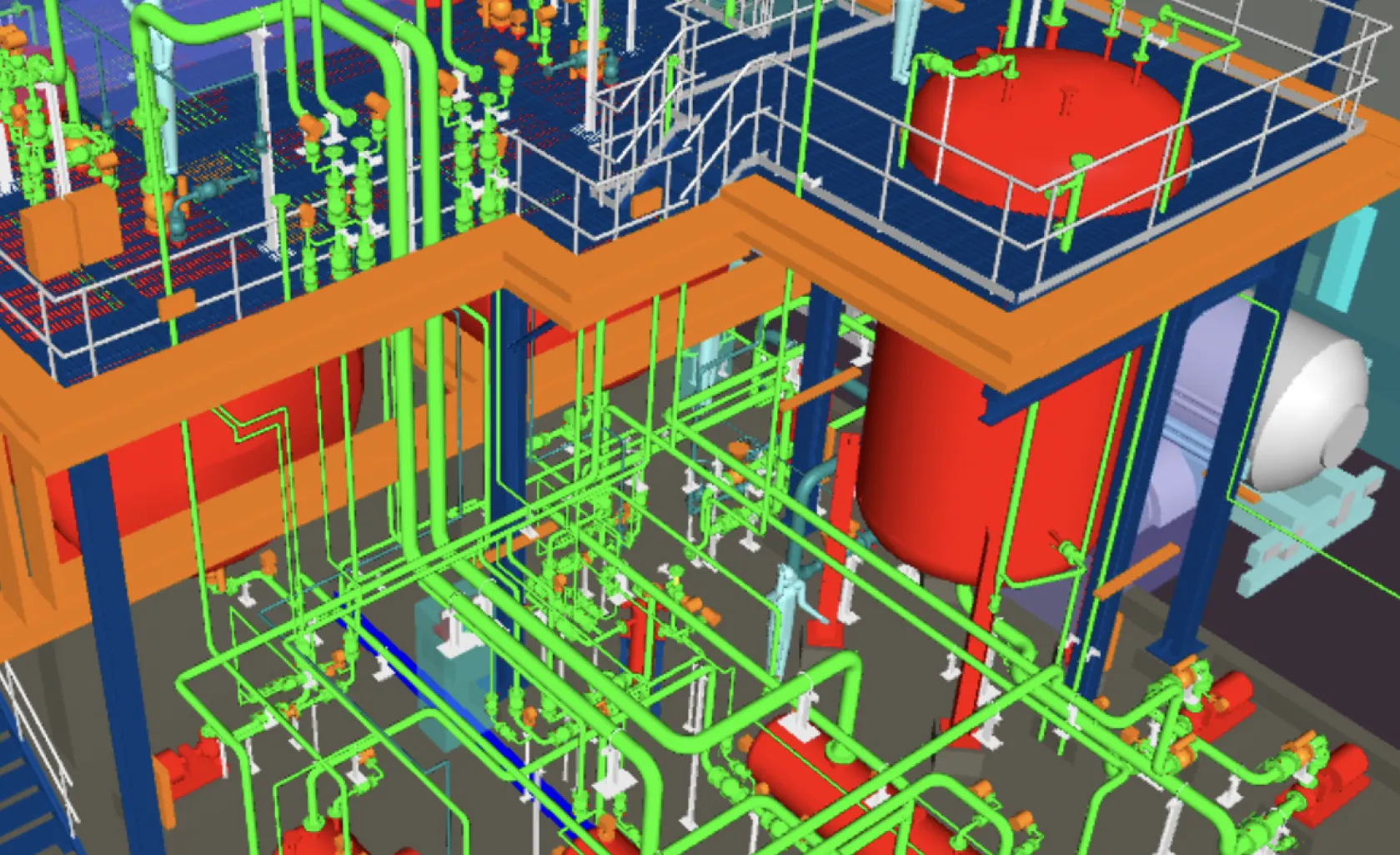
In 2017 a Polymer Additives company announced plans to invest in the expansion of its Amide capacity at their manufacturing site. The expansion formed part of the business’s long-term capital investment plan to satisfy growing market demand for the core product range.
OSL were commissioned to fulfil Detailed Design, Engineering Procurement Construction and Management (EPCM) for the expansion project.
Key Aspects of Delivery
A key aspect of the detailed design package included piping design which required:
- Review of existing pipework specifications
- Design of new piping routing using AutoCAD® Plant 3D software
- Pressure Equipment Directive (PED) 2014/68/EU Assesment
- Design Verification for PED Category III Pipework.
Review Pipework Specifications
Our in-house team of mechanical engineers completed a review of existing pipework specifications to assess suitability for the new pipework system, checks were made, and changes recommended to ensure:
- Chemical compatibility between pipework material and process fluid(s).
- Sufficient pipe wall thickness with regards to the design pressure and temperature.
- All referenced valves were suitable for the design pressure and temperature of the pipework ensuring correct seals, materials, and levels of testing.
- Adequate corrosion allowance for carbon steel pipework.
- Availability of materials specified for pipework, fittings, flanges, and valves.
- Full compliance with ASME code requirements.
Pipework Routing/Design
Using AutoCAD® plant 3D software, our piping engineers were able to model complex pipework routes with accuracy from designed key equipment layout designs. Using 3D modelling software, OSL offers complete design flexibility to simplify design modifications following review meetings with key project stakeholders. For the expansion project, the philosophy was to simplify pipe routing where possible and minimise fitting requirements. As always, safety of onsite personnel was of utmost importance when designing the piping systems. Pipework was designed to ensure:
- Sufficient space to support pipework
- Provision of high vent and low drain points (where required)
- Minimal piping loops for thermal expansion
- Sufficient head room clearance
- Sufficient bridge crossing clearance
- Suitable pipe gradients for draining.
Autodesk Navisworks® 3D models were used for inter-disciplinary information. This enabled the whole engineering team to keep up to date with the latest plant layout.
PED 2014/68/EU Compliance
In accordance with the Pressure Equipment Regulations (PER), OSL ensured full compliance to PED 2014/68/EU for all equipment and piping for the PACE project. The PED applies to any pressure containing equipment above 0.5barg.
The PED design category was determined for each flowline line (typically either Category I, II or III for pipework). The design category is determined from a combination of fluid classification (hazardous or non-hazardous), design pressure and pipework nominal bore. The design category indicates the level of conformity assessment required during fabrication.
For this project, OSL developed the following:
- Essential Safety Requirements (ESR) checklist
- Fabrication Isometrics and drawings of equipment
- Fabricators QA/QC dossier
- Material Appraisal (PMA) form.
- Design calculations (including pipe stress analysis).
Pipe Stress Analysis
Pipe stress analysis was conducted to ensure:
- All pipework was well supported and did not deflect under its own weight (including contents)
- Deflections would be controlled when loads were applied (typically from thermal loads)
- PED 2014/68/EU compliance
- Ensure loads and moments on equipment i.e. vessels, pumps, heat exchangers etc. were within defined allowable nozzle loads
- ASME code stress compliance
- Suitable pipework stiffness to avoid vibration concerns
- Minimise flange leakage potential.
Design review meetings provided a medium for the stress engineer to present potential design changes and discuss options with the piping design team. This enabled OSL to fully design a piping system that was not over stressed, complied with ASME code requirements and justified the system design in accordance with PED 2014/68/EU.
Latest Case Studies
LNG Offloading Terminal Pre-FEED
IM Skaugen (IMS)
Centrica Storage - York Compression FEED
Centrica Storage
LAPS Compression Feasibility Study
A Gas Producer
LPG FEED project
Independent Oil and Gas Company
Pyrolysis Wax Plant Modification Design FEED
Trifol