Pyrolysis Wax Plant Modification Design FEED
in Waste Conversion, Design Development & Implementation, FEED
Share
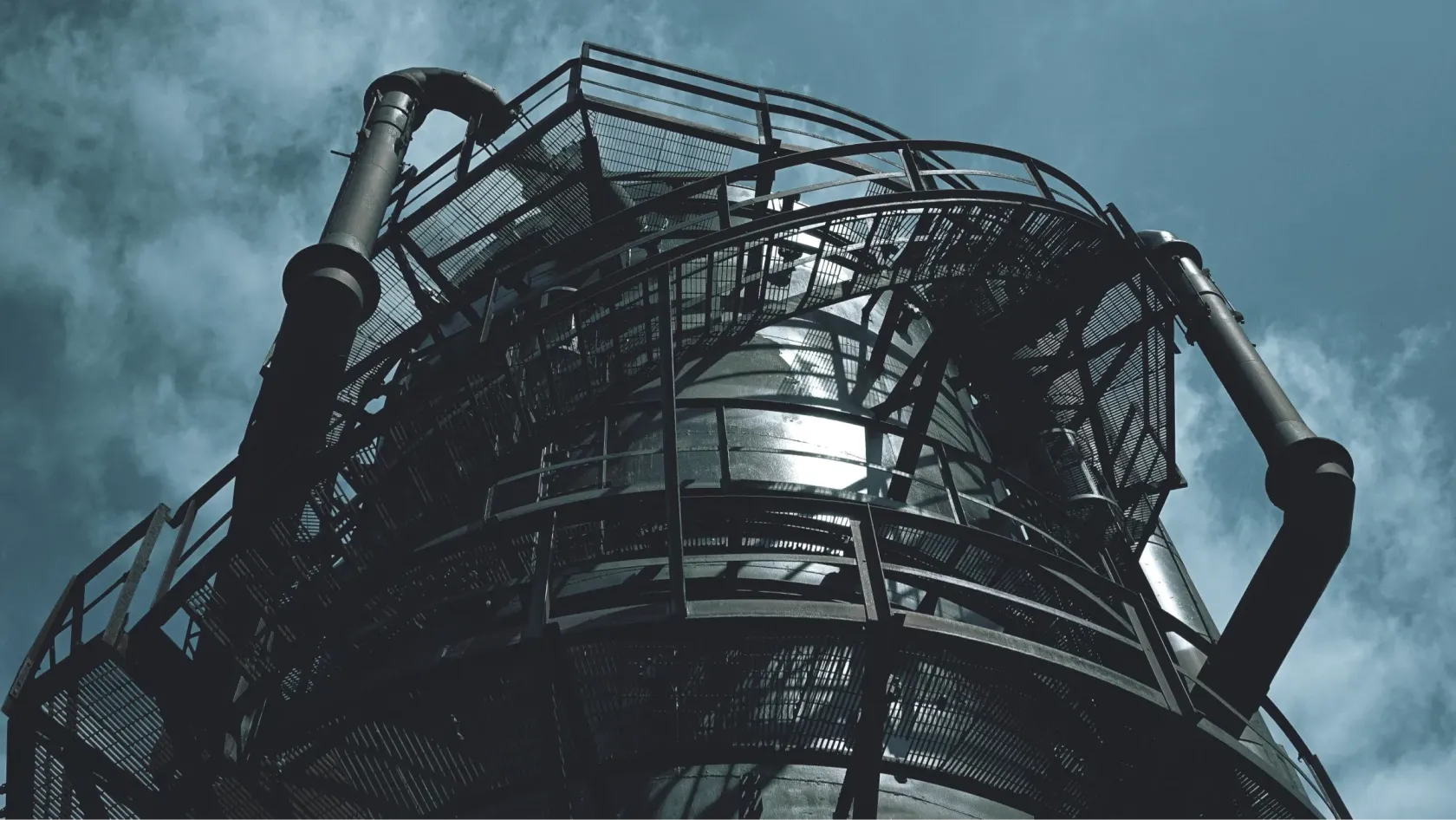
OSL were engaged to undertake design modifications to a commercial scale pyrolysis facility. The plant was formerly used to convert waste plastics into diesel from the pyrolysis of waste polyolefin plastic. However, slack wax (pyrolysis wax) was identified as a more economically viable product than diesel; and therefore the requirement was to adapt the commercial scale plant to produce slack wax.
To achieve this, a number of modifications were required to both the plant configuration and operating conditions with the objective to bypass wax reflux condensers and add a vacuum distillation unit which would further process the product.
Project Overview
OSL conducted a preliminary design and cost estimate and identified testing facilities for slack wax to allow the product to be tested so that the specification could be sold to prospective buyers.
Subsequently, OSL completed a plant modification design on the pyrolysis facility to ensure that the processing plant could produce the slack wax at a commercial scale and meet the product requirements identified during the testing at the pilot plant.
The plant modification design included:
- Design review and modifications of an existing condenser used to partially condense the pyrolysis vapour into wax
- Design of a new intermediate wax tank and cooling system to reduce the temperature of the wax to the required storage temperature before pumping the product to the storage tanks
- Design of storage tanks and transfer loading pump system to transfer wax to road tanker loading.
Key Aspects of the Delivery
Preliminary Design:
- Conducting research and contacting facilities to test the wax product
- Initial plan and cost estimate for a vacuum distillation unit.
Plant Modification Design:
- Modify existing PFD
- P&IDs of new modifications
- Verification of condenser design and sizing
- Verification of intermediate tank design
- Design of plate and frame heat exchanger
- Design of wax storage tanks
- Mechanical drawings and site survey
- Control philosophy for new design and condenser operation modifications
- Civil & structural design for pipework
- Pipe specification checks and new pipe and valve specifications
- Datasheets for new equipment
- Project lists: equipment, lines and valves
- Pipe stress analysis
- 3D models, isometrics and plant layouts
- Carry out HAZOP for the plant modifications.
Clever Thinking®
- OSL identified key design consideration and processing options that would achieve commercial scale production using our structured Clever Thinking® approach
- OSL also highlighted several opportunities to improve the design taking into consideration the nature of the product and its characteristics, and an assessment of the existing site from both safety and operability aspects
- The final design solution met with the specific requirements and limitations set by the Client, as well as complying with relevant codes, standards and safety requirements.
Benefits to the Client
- Project support to identify parties, both commercial and academic to test novel product
- The design study provided the information the Client required to support their financial decision-making process. OSL were able to provide design expertise to enable the Client to gain a better understanding of the plant modifications necessary to meet the new product requirements
- The financial aspects of this project meant that the design had to be done in stages so that funding could be awarded to the Client for different milestones. The OSL team were able to accommodate this and perform the design according to the funding deadline requirements.
Latest Case Studies
LNG Offloading Terminal Pre-FEED
IM Skaugen (IMS)
Centrica Storage - York Compression FEED
Centrica Storage
LAPS Compression Feasibility Study
A Gas Producer
LPG FEED project
Independent Oil and Gas Company
Pyrolysis Wax Plant Modification Design FEED
Trifol