Onshore Compression FEED
in Natural Gas Processing, Design Development & Implementation, FEED
Share
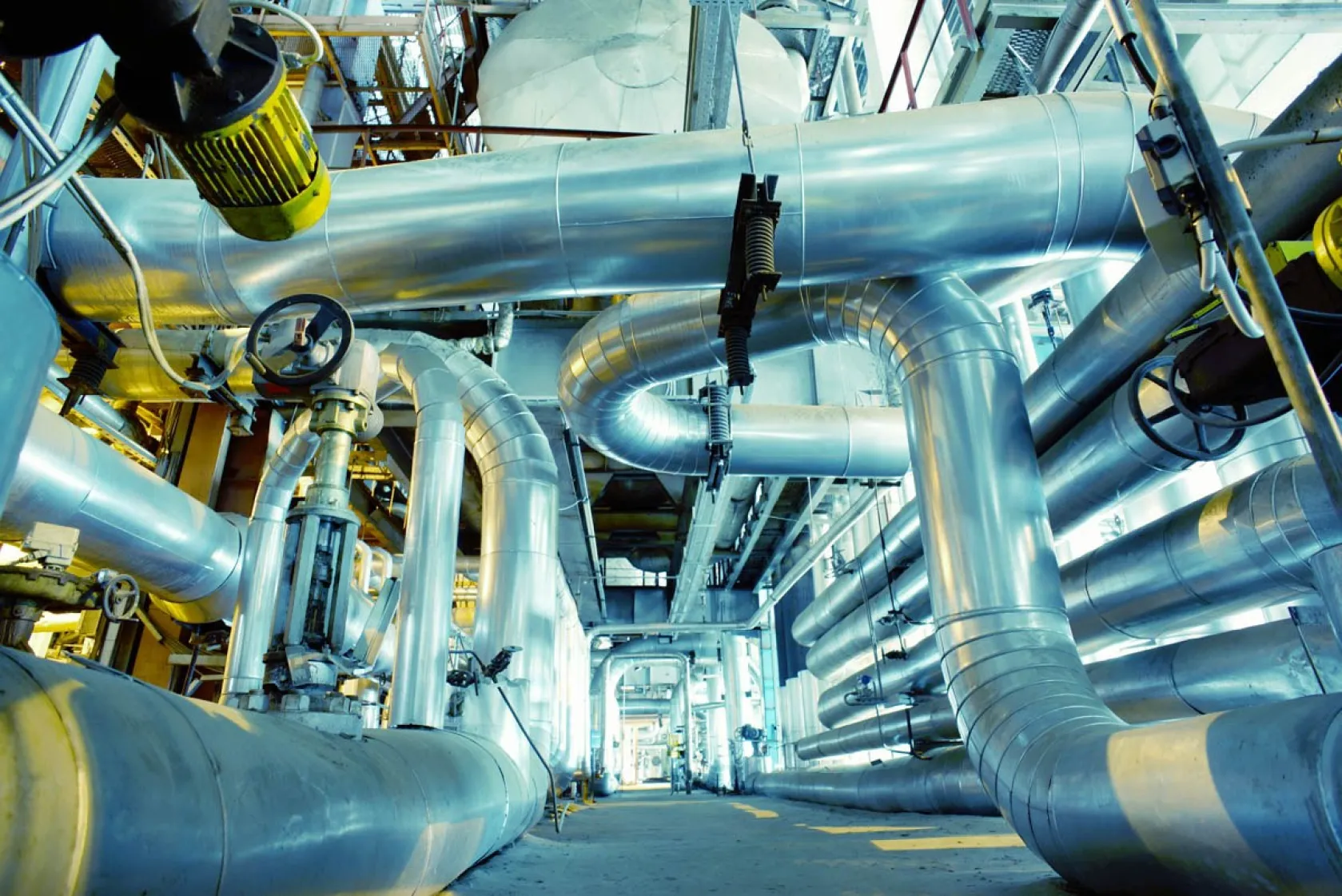
Options were being assessed to improve primary onshore compression at the Operator’s terminal and to remove the requirement for offshore compression. The two options that were taken to FEED were to either install a booster compressor ahead of the existing Field Gas Compressor (FGC) or to rewheel the two bundles within the FGC.
Project Overview
OSL’s first work scope was to carry out a FEED for the booster compressor option, which would initially accelerate production from the offshore gas fields allowing an increase in recoverable reserves, prior to the removal of offshore compression to save OPEX. The booster compressor was to be installed as a pre-compression stage prior to the existing FGC. The FEED study was developed to determine whether this opportunity met the Operator’s economic criteria for implementation, but it was not sanctioned.
OSL were then engaged to develop the design for the alternative option to rewheel the existing FGC with suitable compression stages to meet the conditions of either compressed or non-compressed gas arriving from offshore.
OSL carried out the detailed engineering verification assessments of the onshore plant equipment at the revised operating conditions to identify any necessary modifications to the existing system and prepared a cost estimate for these modifications.
The final element of the project was to carry out detailed design of the required plant modifications identified in the verifications works. This included improved compressor controls and shutdown systems identified by LOPA, revised instrumentation suitable for the new conditions, improvements to the compressor dry gas seal system and a review of the proposed fuel gas safety system modifications. OSL produced full detailed design packages and carried out liaison with the vendors, including liaison and management of the Compressor Vendor in relation to the construction of the rewheel compression stages, construction of an improved coupling guard system and improvements to the dry gas sealing system.
Key Aspects of the Delivery
- Full FEED study of the booster compressor option
- Provision of full technical engineering verification for the preferred option of the rewheel project
- Identification of required modifications and Class I cost estimate (+/- 10%)
- Technical support to verify the chosen compressor curves against the predicted field profiles
- Detailed design and procurement support for the modifications
- Vendor liaison with compressor rewheel vendor and instrumentation and control vendors
- Technical support to the client throughout the project.
Clever Thinking®
Part of the project was to assess the suitability of Operator identified modifications to the compressor fuel gas supply system against the standard BS ISO 21789 (2009) ‘Gas Turbine Applications – Safety’. It was found that the assessment had only included the safety systems that were inside the gas turbine and compressor enclosures and that additional safety systems that were immediately outside the enclosure had been discounted. OSL assessed the system as a whole and proved that this fully met the requirements of the standard and that the systems outside of the enclosure were a viable part of the safety systems. This saved the client significant downtime and capital expenditure required to carry out modifications to the fuel gas supply system.
Benefits to the Client
- Continuing production with the ultimate removal of offshore compression along with reduced offshore operational costs
- Extended field life
- Improved safety and control of the compressor
- Reduced downtime and capital expenditure.
Latest Case Studies
LNG Offloading Terminal Pre-FEED
IM Skaugen (IMS)
Centrica Storage - York Compression FEED
Centrica Storage
LAPS Compression Feasibility Study
A Gas Producer
LPG FEED project
Independent Oil and Gas Company
Pyrolysis Wax Plant Modification Design FEED
Trifol