Fine Chemicals Plant Mechanical and Structural Design
A Fine Chemicals Business, East England in Chemicals, Discipline Engineering, Detailed Design
Share
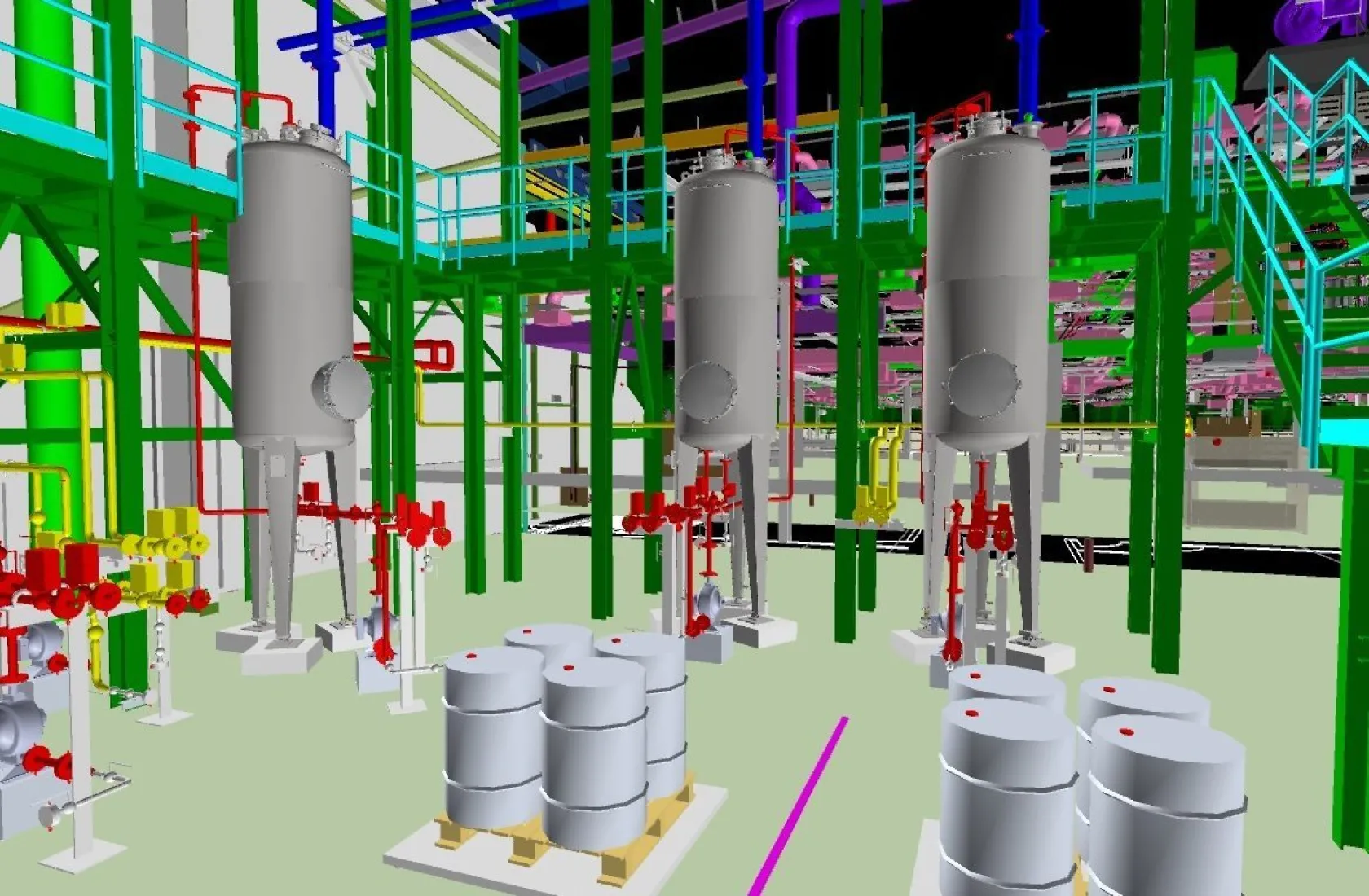
A fine chemicals business in the East of England made a decision to invest in the development of a brand new production facility to enable production expansion and improvements in operating efficiency. OSL were commissioned to support the project and undertake the detailed Piping, Mechanical and Structural design services for new build production facilities and to relocate existing facilities.
Construction of the upper tier COMAH rated facility started in August 2019 with practical completion of the facilities and services targeted for Q2 2021. All work was smoothly delivery during the Covid crisis.
Project Overview
The project was split into two phases:
- Phase 1: Engineering, Procurement and Construction of the new facility
- Phase 2: Transfer of various equipment items from the existing facility for incorporation into the new facility.
The overall OSL delivery was split into 4 key production areas:
- Manufacturing Building
- Plant Rooms
- Tank Farm
- Distillation Building.
The scope of services is summarised as follows:
- Design/ routing of all piping systems totaling approximately 300 lines
- Intelligent multi-discipline 3D modelling of the plant equipment, structures and piping
- Equipment layout for new and relocated plant
- Constructability and design reviews
- Plot Plans
- Civil and Structural Engineering.
Key Aspects of the Delivery
Using AutoCAD® plant 3D software OSL Piping, Mechanical, Civil and Structural engineers were able to develop an intelligent 3D Model that provided:
- An effective tool to evaluate options and aid to communicate both in-house, with the client and other key contractors and vendors
- Ensured sufficient space to safely lay out and install all new equipment and avoid pipework or equipment clashes
- Ensured that all relocated equipment could be safely removed and installed at the new plant
- Ensured that all piperack, pipe bridges and access platforms provided sufficient headroom clearance, bridge crossing clearance and safe access to critical equipment nozzles, valves, and instrumentation.
Clever Thinking®
- OSL used an integrated multi-discipline team approach and secure accessible project IT systems to which the Client had access to give visibility and improve efficiency in decision-making throughout the delivery process
- Developed a dual office approach, seamlessly utilising the key skill sets from OSL’s UK and Spanish operations to ensure the most appropriate team make up for this Client and work scope
- Identified and developed synergies between the Phase 1 and Phase 2 scopes to improve efficiency
- Careful consideration of how the existing plant would be relocated whilst Phase 1 was operational
- Joint constructability review (conducted via video conferencing) with Client and OSL’s UK and Spanish offices which considered the safety, maintainability, and operability of the relocated plant items.
Benefits to the Client
The benefit to the client was OSL’s ability and flexibility to provide concise solutions to the delivery of the project. With particular focus on the “Relocation” scope resulting in the safe removal and subsequent installation.
Developing the synergies between the Phase 1 and Phase 2 scopes in parallel ensured a cohesive and efficient design, avoiding space issues on piperacks and less than optimal routing. Phase 2 issues were identified and addressed early, resulting in reduced construction effort.
OSL’s robust procedures and use of a central project sharing site (SharePoint) provided the Client with the reassurance to progress the project and work collaboratively during a difficult period of time due to the implications of COVID and Brexit.
Latest Case Studies
LNG Offloading Terminal Pre-FEED
IM Skaugen (IMS)
Centrica Storage - York Compression FEED
Centrica Storage
LAPS Compression Feasibility Study
A Gas Producer
LPG FEED project
Independent Oil and Gas Company
Pyrolysis Wax Plant Modification Design FEED
Trifol