Gas Storage Facility EPCM
EKB, Germany in Natural Gas Processing, Design Development & Implementation, EPCm
Share
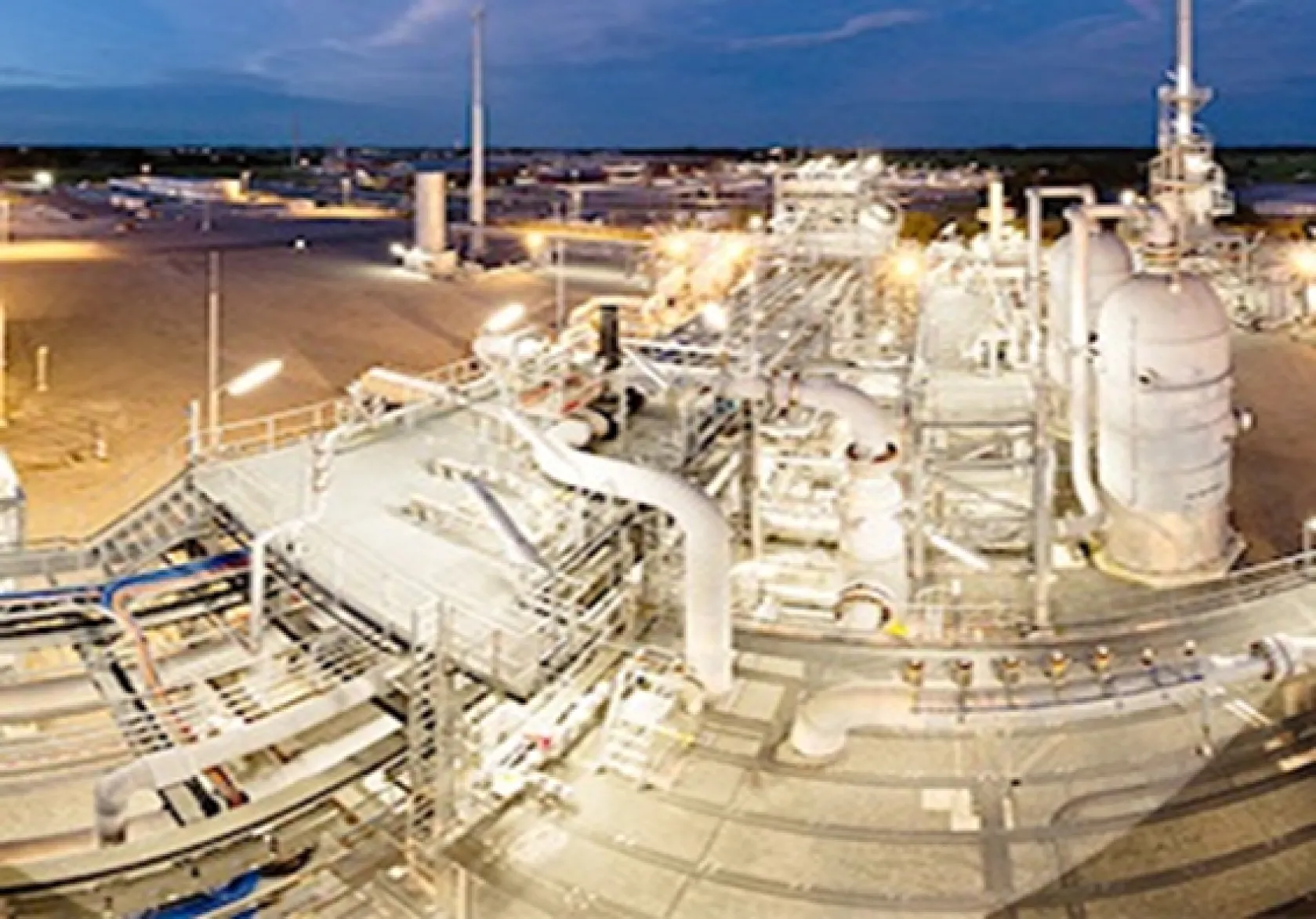
EKB was a joint venture company formed between BP, Dong Energy (now Orsted) and Gazprom Germania; to design and operate a major underground gas storage facility located at Etzel, in North West Germany.
Connected via a 60km pipeline to the Dutch gas transmission system, the facility would provide access to one of the most important natural gas trading hubs in Europe.
Project Overview
The project comprised seven underground salt caverns, well heads and pipeline manifold, flow lines, gas compression (3 x 8MW high speed electric drive units with VSDs), gas dehydration, heating systems, fiscal metering, vent and blow-down, utilities, safety systems, control systems, electrical infrastructure, lighting, earthing, lightening protection, operations and maintenance building, security and telecoms. The project represented a capital investment of €275mm and took 4 years to design, procure, fabricate, construct, and reach commercial operation.
Key Aspects of Delivery
OSL initially provided the technical assurance team to oversee the detailed design development, but later performed detailed design.
On behalf of the client, OSL oversaw a joint venture design team of Technip/AMEC, and managed contracts and procurement. OSL provided project management (commercial and technical assurance), project management reporting and liaison with EKB’s partners. As the design progressed, OSL were asked to undertake significant elements of the detailed design including control and instrumentation and electrical elements. The senior OSL technical team moved to site to oversee the construction, commissioning, testing, operational training, documentation, and handover.
Subsequently, OSL developed and implemented several technical enhancements to improve the operation and performance of the facility. This included concept development and estimating, detailed design, procurement, construction, management, commissioning, document control and close out.
Clever Thinking®
Aside from the uniqueness of this project, some of the equipment selected perfectly reflects OSL’s skills at innovative problem solving. The gas compressors selected were hermetically sealed, gas cooled units fitted with magnetic bearings, which avoided the requirement for the complex oil and seal systems generally found with these machines; together with all the attendant maintenance these systems require. The use of such a machine was a first for BP and it was hoped to be the pilot for many other applications, including subsea. The use of magnetically suspended variable speed 8MW electric motors to drive these gas compressors meant that the plant could start-up from cold in just a few minutes and switch between exporting and importing gas very quickly, thus maximising the ability of the gas traders to buy/sell in response to market variations.
Benefits to Client
The benefit to the client was our ability to provide a range of services at each stage of the project from concept design through to implementation and plant operation. We were able to ensure continuity and flexibility in the team from a technical and commercial perspective, which not only provided the client with the assurance required throughout the project development, but it also allowed us to identify where improvements to the operation could be made, based on the actual operating conditions experienced after start up.
Next: Onshore Compression FEED
Latest Case Studies
LNG Offloading Terminal Pre-FEED
IM Skaugen (IMS)
Centrica Storage - York Compression FEED
Centrica Storage
LAPS Compression Feasibility Study
A Gas Producer
LPG FEED project
Independent Oil and Gas Company
Pyrolysis Wax Plant Modification Design FEED
Trifol